- Joined
- May 1, 2013
- Messages
- 10,668
- Reaction score
- 6,561
- Location
- Dublin
- Country
- Ireland
- Dash Cam
- Street Guardian UK / EU / EEA Distributor
About year ago I was thinking about similar Interesting approach / design dash camera that could be mounted over mirror bracket. Now somebody read my mind and made it
. Maybe not fully 100% what I had in my mind ,but approach is quite similar what I thought.
According to correspondence table it fits over 200 different car makes / models.
It can be connected to car multimedia system or any other portable external display that has Video RCA AUX Input for operating and file viewing.
Although specs are not that great ( only 720p ), but mounting idea is interesting.
Similar approach has been already take by OEM VW and Audi .
If only they could use much better hardware and higher specs, then for sure it would be popular on the western dash cam market. Of course we can not call it fully discrete installation, but at least its right in the centre of the wind-shield and not obstructing driver view, also buttons to operate are easy to reach.
Price ins China is about 90usd

According to correspondence table it fits over 200 different car makes / models.
It can be connected to car multimedia system or any other portable external display that has Video RCA AUX Input for operating and file viewing.
Although specs are not that great ( only 720p ), but mounting idea is interesting.
Similar approach has been already take by OEM VW and Audi .
If only they could use much better hardware and higher specs, then for sure it would be popular on the western dash cam market. Of course we can not call it fully discrete installation, but at least its right in the centre of the wind-shield and not obstructing driver view, also buttons to operate are easy to reach.
Price ins China is about 90usd

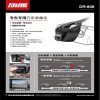





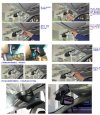


Last edited by a moderator: